“Twenty years from now, you will be able to buy a piece of land and print your own home through an app on your phone,” says Andrew Logan. “That is the future.”
Logan Architecture is testing 3D-printed homes, using robots to build walls in additive layers as an alternative to conventional construction methods. Two of Logan’s designs were realised this year in his home city of Austin, Texas. One was a development of four two-storey houses in the east of the city, completed in September.
Their lower storeys were printed on site by a nozzle suspended from a mobile overhead gantry. Directed by software, the machine piped parallel narrow beads of cement, like toothpaste on a brush, layer on layer. Larger timber-frame second storeys were then constructed on top of the printed walls.
Logan says 3D printing brings the freedom to design curved walls and corners — “more receptive to human circulation” — without worrying about the highly paid tradespeople required with traditional methods. The technique has limitations, says Logan: there is a maximum wall height of 8ft 5in and drilling holes to hang photos might be messy and time consuming — he installed picture rails on all the walls.
Features such as the vaulted master bedrooms and cedar cladding of the East 17th Street houses allowed their developer, 3Strands, to market them at more than $400 per sq ft, about 25 per cent above the median price for Austin recorded by Realtor.com.
Across town, Logan’s other 3D design shows how being able to build dwellings quickly and cheaply has potential for social housing. Six one-bedroom 400 sq ft homes for the charity Mobile Loaves and Fishes, printed three at a time in a few days, form part of a project to rehouse Austin’s homeless population.
The cost advantage of printing over construction methods dependent on human labour could drive the technology’s acceptance for mid-market housebuilding. Developer SQ4D printed and sold a three-bedroom, ranch-style house in the town of Riverhead, Long Island, this summer. It cost $20,000 but would have cost $150,000 using conventional methods. “We listed it for $299,999,” says Kirk Andersen, SQ4D’s director of operations. “There are houses in the area that go for $550,000, so it’s almost 50 per cent below.”
SQ4D was formed five years ago by Andersen and three fellow construction engineers to test the potential of additive manufacturing for residential property. “We literally took a small 3D plastic printer and scaled it up . . . We pushed some concrete through it and we said, ‘This is a real thing; we can actually do this!’ ”
Two trial structures in 2017 and 2018 were used to refine the printer and the mix of sand and Portland cement that it pipes. “We learnt a lot about hoses,” says Andersen. “We started out with an inch and a quarter [nozzle] but it’s like a clogged artery, it starts to get smaller and smaller.” Weather conditions are another consideration: on hot days the cement can dry too fast and develop cracks. “You need to keep it hydrated,” he says. “We have misting systems.”
SQ4D uses a bespoke 32ft wide x 12ft tall gantry printer, which can be assembled on site in six hours. The external and internal walls of the Riverhead house took 48 printing hours with only three operatives on site to oversee the machine and cut the apertures in the wet cement for windows. Andersen estimates a conventional build for the same structure would have taken 10 weeks.
As well as being faster and cheaper, Andersen says the robots could improve construction health and safety — the industry is notable for its accident rates. The environmental impact of printing houses is still up for debate. CO2 emissions from cement production are high and, though there are studies suggesting a smaller carbon footprint for 3D-printed structures, they used poured concrete walls as a comparator rather than brick or timber. Andersen says SQ4D is investigating using recycled crushed concrete in its mortar and even pumping CO2 generated during the mixing and printing back into the concrete for storage.
The only clue to the Long Island house’s construction is the piped striations in the exterior walls. “People call it a corduroy wall,” says Andersen. “Those lines are the story of how your house was built.” But Andersen’s interest is primarily in the speed and economy of the new technique rather than its design potential: “We don’t want a crazy abstract house at the moment, we want it to be relatable.”
Elize Lutz and Harrie Dekkers live in a structure that realises more sculptural possibilities. In August they became the first tenants in Europe of a fully 3D-printed house. Their 1,000 sq ft boulder-shaped bungalow is one of a planned five properties in the Meerhoven district of Eindhoven, in the Netherlands, collectively known as Project Milestone. The scheme is a co-venture between the city authority, the Eindhoven University of Technology, Vesteda, a property investor focused on mid-market rental housing, and Saint-Gobain Weber Beamix, the specialist concrete maker that developed the 3D-printing system. The single-storey structure was printed in 24 sections by a robotic arm a mile away in Weber Beamix’s factory, then assembled on the wooded Milestone plot.
Lutz and Dekkers, retired jewellery shop owners, were living in Amsterdam when Lutz saw a call for applications to become trial tenants. It appealed to the couple’s sense of adventure, she says: “I like to live in spaces that are special, and it was a neighbourhood I didn’t know.”
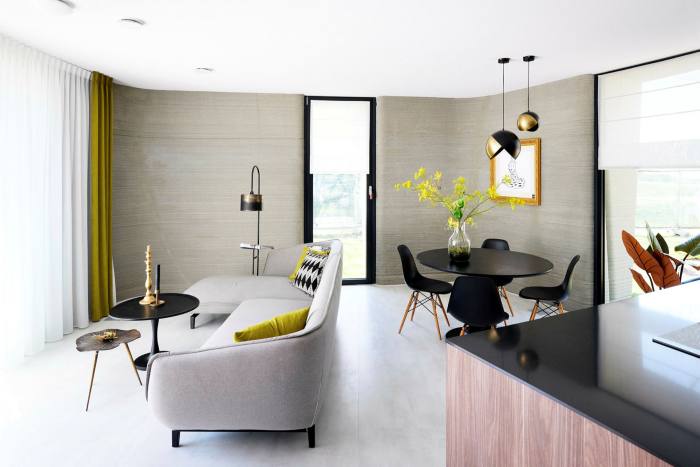
Three months in, they are enthusiastic ambassadors for the house’s open-plan layout and curves. “It’s all a bit round, everything is organic forms; it’s playful,” says Lutz. “You never get bored,” adds Dekkers. As with all 3D-printed buildings, the walls are a cavity construction. Lutz says their 7in thickness makes them feel “like an old castle — it gives you a very safe feeling”. Otherwise, they say, there are few differences from living in a conventional property.
Gian Sterken, Weber Beamix’s 3D sales project manager, says the couple’s feedback is informing the final design of the second house, which should be completed next year and will rise to three storeys in an obelisk shape. Others are pressing ahead too. Icon, the company that printed Logan Architecture’s designs, has announced a project to print 100 homes in Austin next year. SQ4D is building new printers and talking to municipalities across the US.
Building sites staffed solely by what Andersen describes as “a guy with his feet up babysitting a machine” may not become the norm yet. But those corduroy walls could soon be a common sight.
Follow @FTProperty on Twitter or @ft_houseandhome on Instagram to find out about our latest stories first